For decades, the manufacturing sector has been known to be driven by legacy processes, and is infamous for its complexity. Given the myriad of aspects involved – right from the supply chain, operation, to logistics and customer delivery, it has become critical for the manufacturing industry to make meaningful data connections between each process in order to thrive. It is at this juncture that business intelligence (BI) comes in to bridge the gap between systems and enable a data-driven approach to decision-making in the manufacturing process.
As per research from Markets and Markets, the demand size for Business Intelligence will grow from USD 23.1 billion in 2020 to USD 33.3 billion by 2025, at a CAGR of 7.6% during the forecast period. The report further states that the expansion of BI has been fuelled by factors such as greater investments in analytics, higher demand for dashboards, increased focus on digital transformation, growing cloud usage, and IoT in supply chain and other industries, including manufacturing.
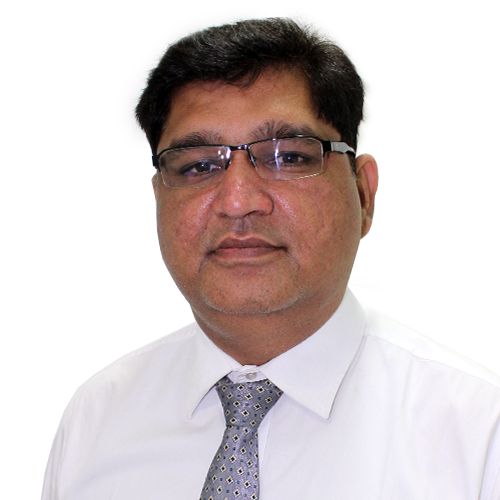
Understanding BI for manufacturing
At its core, BI refers to the various programs, tools, and processes used to analyse data and provide insights that might help an organization make better business decisions. Hence, one can safely concur that digital transformation and BI are deeply linked.
Within the manufacturing space, BI enables companies to bridge the gap between systems, and supports a data-driven approach to decision-making in the process. This is of particular importance, in cases where manufacturers still make commercial and operational decisions using spreadsheets and observational approaches. This strategy may result in ‘after the fact’ decision-making based on outdated data. And hence, manufacturers must adopt developing technology to stay competitive in light of recent events and the shifting business landscape.
From losses to profits- the BI way
Validating the need for BI within the manufacturing sector, a leading apparel manufacturer that followed traditional processes faced a challenge where multiple errors were made while capturing customers’ data. Furthermore, consignment tracking became a big concern, leading to losses throughout transit and storage, and eventually culminating in a business loss.
As a solution, BI specialists constructed data warehouse that provided maximum production and distribution efficiency. With this, the manufacturer was able to generate real-time reports of the sales and inventory, even during transit, and could also efficiently plan and forecast analysis of peaks and downfall in demand as per season.
Through this, they were able to achieve maximum production and distribution efficiency, which was crucial in increasing the company’s profit margins.
BI has also proven its merit in helping manufacturers enjoy seamlessness across business functions. In the case of a manufacturing subsidiary, following a company restructuring, the management felt the need to simplify and unify information access across their complicated worldwide environment. Within the firm, executives were unable to access essential KPIs and reports to fully govern the business due to various reasons. As a solution to this, BI experts presented a workable data model for structured reporting that incorporated best practices. With this, the teams were able to immediately understand and appreciate dashboard functionality, multi-dimensional reporting, drill-through capabilities, and ad hoc reporting. Additionally, they were also able to dig deeper into trends, correlations, and core reasons for sales performance, and bring in improved efficiency in operations.
The way forward
While the adoption of BI in the manufacturing sector is relatively nascent, its future looks bright. BI platforms will transform the process of decision making across industries. Hence, new-age manufacturers will favour certainty over uncertainty and action over inaction to take the industry to new heights.